Welcome to the official homepage for the Max-i fieldbus and Max-i Association
Overview
Max-i is a new, extremely powerful and efficient multi-master fieldbus, which enables the lowest automation and LED-lighting costs ever seen combined with maximum performance, reliability, failure tolerance and safety! It may be regarded as a combination between a highly improved CAN bus with a high-power 20-V power supply running on standard installation cables and some hardware-based I/O objects to handle the most commonly used functions like:
- UART interface to microprocessors and displays with light control.
- SPI interface to for example sensors, servo motor controllers, displays with light control and mechanical functions for lamps like pan and tilt.
- 4-bit Boolean (on/off) I/O with possibility for:
- 24 bit or 32 bit data for timestamp or for example for a countdown display (transferred by means of SPI).
- Inrush current limiting with selectable time constant.
- Group light control for traffic lights, control lamps and signal towers.
- A/D conversion with programmable gain and offset to convert sensor values to SI or Imperial units.
- D/A conversion.
- Lock control with keypad scanning and light control.
- Very advanced LED driving as described on page "Advanced LED Lighting".
Max-i may be used for virtually all low to medium speed applications (up to 25,000 telegrams per second on short lines) like:
- Green smart house systems, building automation, alarm systems and access control.
- Advanced LED lighting including professional stage light, architectural lighting and traffic lights.
- Industrial automation including motion control, robots, cobots and safety applications up to IEC 61508 SIL 3.
- Transportation applications such as automotive, special vehicles, railway, ships and aerospace.
- Internet of Things - IoT.
- Military applications including equipment, which must survive very strong electromagnetic pulses.
Max-i has a lot of outstanding benefits:
- It is possible to make a complete bus interface in one integrated circuit (IC), which is small and cheap enough to be built into even the smallest and most price sensitive actuator, sensor or lamp, gets its supply voltage of 20 V (15.4 - 25.2 V) directly from the bus and only needs an absolute minimum amount of external components - often only a few small ceramic capacitors. This voltage range covers standard 24-V (+5 %) industrial and railway applications, but 20 V is selected as the nominal voltage for more reasons:
- It the highest voltage, which cannot generate a dangerous arc in high current applications such as smart-house systems. At 20 V, a creepage and clearance distance of 1 mm is enough to extinguish an arc, but at just 28 V, which is the charging voltage of a 24-V battery, arc lengths up to 12 mm are possible at 50 A and household batteries can easily supply several kA - see Annex D in the Max-i specification for further details.
- It is the highest voltage, where the power in a switching arc is too low to destroy gold plated contacts.
- It has become the de-facto standard for the charging voltage of mobile phones and computers. This makes it possible to omit most chargers and just connect the devices to a 20-V outlet. In the future, an 18-V battery, which has a charging voltage of approximately 21 V, would for this and many other reasons such as driving LED lamps be much better suited for passenger cars than the present 12-V standard.
- It fits very well with 18-V brushless motors, which has become the de-facto standard for most electrical hand tools and some window openers.
- It makes it possible to accept big voltage drops on the line, which may occur during load switching. This also enables long distance communication on thin cables and telephone lines.
- The hardware-based architecture gives a much higher reliability and failure tolerance than any fieldbus, which need a microprocessor on the sensor, actuator or lamp side. This is achieved by means of a unique dual-phase clocking scheme for all flip-flops, which makes them tolerant to very big propagation delays and changes in transistor data, a rugged RC-oscillator (no crystal needed) and an absolute minimum amount of transistors. The present Max-i implementation uses only approximately 6,000 gates including all the different I/O objects corresponding to approximately 40,000 transistors. As a comparison, even the smallest ARM Cortex-M0 microprocessor uses approximately 12,000 gates, and if just a single transistor fails or there is a bug in the program, you can lose everything. With Max-i, you will only lose the function(s) that transistor is a part of and there is no software to go down and no program memory to lose charge over time, which may especially happen at high temperatures.
- It is possible to use cheap, standard, unshielded and un-terminated installation cables instead of special communication cables. This saves a lot of money and troubles with shield connection and shield currents and makes it possible to transfer much more power over the bus than any other fieldbus - up to over 1 kW.
- It uses bit-wise bus arbitration, which has many very important benefits compared to any other access method:
- It is the only multi drop technology (not point-to-point), which does not need any reconfiguration when devices are added or removed, so this may happen at any time on the fly. In all other systems, a new device needs to be inserted in the communication sequence before any direct communication is possible, and if a device is removed without reconfiguration or fails, time is lost forever.
- The response time is much faster for the same speed as a device does not need to wait for a poll, a token or a time slot before it is allowed to send a message.
- The bandwidth utilization is much better since no time is lost on devices, which do not need communication.
- The failure tolerance is much higher since there is no dedicated master or leader unit and no need for a centralized database. Since Max-i uses voltage clamps in each device instead of resistor termination, the cable may even be cut in two or more parts and each part can still work if it is powered up.
- It is possible to use many different protocols simultaneously. It is for example possible to run any CAN protocol like DeviceNet or CANOpen together with the Max-i protocol and in this way save extra cables and communication channels.
- The signal integrity is always very good, which is not the case for most other fieldbus systems based on bit-wise bus arbitration like CAN:
- All bits are 100 % symmetrical even under bus arbitration (dominand and recessive bits) so unlike for example CAN there is no bias distortion and no problem with ringing on recessive bits.
- All signal levels use a virtual midpoint between the supply rails L+ and L- as reference and therefore do not change due to voltage drops as long as the cross section of the two supply lines L+ and L- is the same.
- The triggering levels are always in the ideal point in the middle between the positive and negative pulse levels no matter the signal attenuation. In CAN, they are typical fixed to 0.5 V and 0.9 V compared to the negative supply rail, which may cause asymmetry both in case of varying signal amplitude and in case of voltage drops.
- There is very limited oscillation due to propagation delay between devices during bus arbitration and it is not necessary with a fairly high driver output resistance (loss) to limit this to an acceptable level.
- It has an excellent ratio between signal and noise and between transmitted power and lost power.
- The signal integrity does not depend on termination resistors and is therefore usually not destroyd in case of a line break, and busses may be connected and disconnected at any time. This may for example be very useful for trucks and trailers and connected train sets.
- Since there are no termination resistors, it is possible to utilize reflected wave switching at a reduced speed to enable long distance communication on thin communication lines up to 20 km, make it possibe to use free topology instead of a trunk line and make it possible with a very large number of devices (high capacitive load) on the same bus such as a sensor and indicator for each parking bay in a car park. Other fieldbus systems (without the unique voltage clamps of Max-i) must either be designed for high-speed communication on a trunk line like CAN or very low speed communication with free topology like DALI and can't do both.
- It uses the very efficient publisher-subscriber model, where it is the various values, which have an address/identifier, not the various devices. There are many very important benefits of this:
- The same value may be utilized simultaneously by any number of devices. This is extremely practical for example for display systems, traffic lights and synchronized multi-way landing switching of lamps.
- Since the majority of telegrams only contains simple, standardized values, all features of present and future devices can be utilized without any limitations. It is just a matter of reading the data sheet of a device to see which data it publishes and which data it subscribes to. It is therefore not necessary to specify and standardize device profiles for lamps, blinds, HVAC control, door locks etc. so there is no need for complex abstraction layers like OPC UA or Matter.
- It is not necessary to add a long list of source and destination addresses when gateways are used.
If the publishers and subscribers (clients) are not connected to the same bus, MQTT brokers (see https://en.wikipedia.org/wiki/MQTT ) may be used to establish world-wide communication over TCP/IP and decouple the various clients so that they need not to be online simultaneously.
- It is extremely efficient - probably the most efficient fieldbus in the world:
- With the short 12-bit identifier, a 4-bit value can be transmitted in only 5 bytes including a 20-bit CRC-check to detect errors, a 7-bit Hamming code on the identifier to protect against masquerading, a data type and an optional 8-bit telegram serial number for safety applications. Even with the long 31-bit (PNS) identifier, a process value with 20-bit mantissa and 8-bit exponent, scaled to SI-units only requires 9 bytes.
- It does not take longer time to poll a value than to send it event driven if the value is generated by the Max-i controller or loaded into it through the SPI interface. The poller just sends the identifier and the receiver then completes the message in very much the same way as if it has won a bus arbitration. This is especially useful in combination with multiple subscribers like traffic light lamp groups. After an update, you probably want to check the lamp status, but if this is reported automatically (event driven), a lot of bus arbitration may take place and it may overload the receiver. In such a case, it is much easier and equally fast just to poll the status.
- It is possible to transmit data to more devices in the same telegram for example to stage lamps and to servo axes in CNC machines, robots and cobots. On a 25 m trunk line, Max-i is able to synchronize over 16 servo motor axes with 32-bit precision to an accuracy of 0.1 μs at an industrial state-of-the-art communication cycle of 400 μs. This is much faster than CAN and close to or even better than the performance of a much more expensive and complex Ethernet solution, which also has much lower reliability due to the necessary routers and other complicated electronics. In case of short messages, Max-i outperforms single pair Ethernet (10BASE-T1S) on all parameters including speed, response time, reliability and price as decribed on page "Industrial Automation"! With Max-i, it is no problem to get robots to work together as cobots as they can just use the same telegrams.
- It uses synchronous communication with a unique, self-clocking bit coding, which is as efficient as Manchester coding during bus arbitration and 1.2 times more efficient after that and cannot get out of phase synchronization.
Efficiency is a much better means to get many data through than speed because it does not reduce the signal-to-noise ratio (S/N) and therefore does not increase the error rate! If for example the probability of a bit failure (p) is 10-7, which is usually accepted in a field bus system, just a factor 2 (N) increase in speed will reduce this to approximately p(1/N) = 3.2 x 10-4, which is unacceptable.The S/N is the ratio between signal power and noise power, but for digital communication, S/N = (Eb/N0) x (Fb/B) where Eb is the energy (power x symbol-time) in each bit and N0 is the noise power per Hz or noise energy accumulated over the time of the bit. Eb/N0 is called the normalized signal to noise ratio or signal to noise per bit. Fb is the number of bits per second (channel data rate) and B is the necessary bandwidth to transfer these bits. Fb/B is therefore a measure of the efficiency of the communication and is the reciprocal of the so called "gross" link spectral efficiency. The more bits, which can be transferred for a given bandwidth, the better. For NRZ with square pulses, which is used by most RS-485 systems like Profibus and MODBUS, Fb/B may be set to approximately 0.7, and for Max-i, it is approximately 0.5. Note that the total denominater N0 x B is the total noise power, which is let through by the bandwidth.Fieldbus systems like for example Ethernet and Profibus DP may look fast at first glance with their respective data rates of 100 Mbit/s and up to 12 Mbit/s, but for many practical applications, the S/N may be over hundred times lower for the same or even lower throughput due to low efficiency and often an enormous overhead - especially if IPv6 is used with its 128 address bits, which alone is approximately twice as long as an average industrial Max-i telegram with the long identifier!On for example a 100 m trunk line, it takes Profibus DP 1.14 ms to exchange 5 output data bytes and 5 input data bytes with 32 devices at 12 Mbit/s (32 x (317 + (10 x 11)) / 12,000 ms = 1.14 ms) according to the Design Guidelines. The average response time to an event is therefore approximately 570 µs, and because Profibus uses a transmission line with a characteristic impedance of 135 - 165 Ω (150 Ω in average), a 172 Ω active termination resistor network in each end (2 x 390 Ω in parallel with 220 Ω) and RS-485 communication with a dedicated Profibus transceiver like LT2876/LT2877, which has a differential pulse amplitude of 5.4 V under these circumstances, the energy Eb in each pulse on the line is ((5.4 V)2 / 150 Ω) x 83.3 nS = 16.2 nJ.As a comparison, it only takes Max-i 180 µs to transmit 5 bytes event driven (or polled) on a 90 m, 50 Ω, balanced 4-wire line at a signal level of 13 V and a pulse width of 1 µs so Eb = ((13 V)2 / 50 Ω) x 1000 nS = 3400 nJ.Under these circumstances and if N0 is considered constant, Max-i therefore has a 570 / 180 = 3 times shorter response time than Profibus DP at a (3400 x 0.5) / (16.2 x 0.7) = 200 times better S/N! In practice, the difference is even bigger because the coupling impedance of noise is inversely proportional to the frequency, so when the band width B is increased, much more noise is let through! Probably due to the low S/N at 12 Mbit/s, the Design Guidelines of Profibus DP recommend that if absolut minimum response time is not needed, the speed should be maximum 1.5 Mbit/s, which may be used up to a line length of 200 m. This makes Profibus DP further 4 times slower than Max-i for the same line length - a total of 12 times and still with at least 25 times lower S/N. If there are less devices than maximum on a segment, the response time of Profibus DP will of course be shorter as the formula shows, and if more segments are connected together as a line and/or there is also slave to slave or asynchronous communication, it will usually be longer. Due to the event driven nature of Max-i, the responce time is almost unaffected by the number of devices for most practical process control systems!Speed is really nothing to strive for for several reasons:
- It reduces the energy in each pulse and with that the S/N, which has an enormous influence on the error probability as shown above.
- It reduces the possible transmitter voltage if the slew rate (V/µs) should be resonable. An N-time reduction in speed may allow an N-time higher voltage for the same slew rate, which gives a N2-times better S/N and makes it much easier to burn through contact corrosion in connectors.
- It may create problems with spur cables. As a roule of thumb, the length of spur cables should be less than the rise time of the pulses divided by 6 times the propagation delay per meter of the spur cable. If for example the rise time is approximately 120 ns, as it is the case for Max-i, and PE cables with a propagation delay of 5 ns/m are used, spur cables up to 120 ns / (6 x 5 ns/m) = 4 m is allowed, but in practice even longer spur cables may be used, and Max-i may even use reflected wave switching at a reduced speed to allow free topology. Profibus DP does not allow spur cables at all, which may be very impractical.
- It increases the necessary receiver bandwidth and therefore let more noise through, and since the coupling impedance of noise is inversely proportional to the frequency, high frequency noise from for example variable speed drives are much more serious than low frequency noise. As a result, it may be necessary with a lot of restrictions about cable spacing and how the cable must be drawn and connected, as it is the case for Profibus DP.
- It is extremely safe. It is the first fieldbus designed directly for highly demanding safety applications according to IEC 61508 SIL 3 (death of 1 - 3 people) without the use of additional protocol layers or safety monitors. Because the 4-bit Boolean data type is handled entirely in hardware, which is much more predictable than software, the requirements in IEC 61508 is 10 times lower for a given SIL level than a software solution. A selectable telegram serial number counter makes it possible to detect lost messages and/or telegrams inserted by hackers.
- It is fully deterministic. A "babbling idiot protection" prevents high priority devices from taking over the bus as it is possible with CAN and if all devices want to transmit simultaneously, they just get through one by one and a telegram watchdog by default prevents telegrams with more than 1028 data bytes.
- It is possible to change the published data temporary. This is extremely practical during commisioning where it for example makes it possible to simulate the presence of material and test the response to an exceedance of an alarm limit without the need to force the alarm condition.
- It has a remarkable and unusual simplicity that will please everyone from makers to professionals. There are just a few registers to setup and it is not necessary to add complicated layers like OPC UA or Matter to make it possible to interpret the data. All values have a specified data types and may be scaled to SI-units and a new numbering system (PNS) makes it possibe to identify them directly as properties of the equipment to which they belong like for example HX127AT4 for Heat Exchanger 127A Temperature 4. The Max-i specification fills only approximately 250 pages where approximately half is used for background material and annexes. As a comparison, most other fieldbus systems have specifications way over 1000 pages and OPC UA consists of 14 documents with a total of 1250 pages.
- Since the protocol is handled entirely in hardware, which cannot be changed, there is no needs for an expensive and time consuming conformance test and it is much easier to fulfill the requirements of the European Union Cyber Resilience Act (CRA). For the majority of applications, you just buy a chip (when it becomes ready), copy a hardware application note and maybe a PCB-layout and you are ready to sell and don't need production time to load a program. With a software solution, it can take months to meet and document compliance with the requirements of the CRA directive especially if open source software is used such as Linux and many standard libraries. CRA requires due diligence, documentation, and vulnerability assessment, so you can no longer pull in an open source component without knowing what it contains.
"Perfection is achieved, not when there is nothing more to add, but when there is nothing left to take away."
Antoine de Saint-Exupéry
The name Max-i means Multiple Access Cross (X) coupled interface. It refers to Max-i being a multiple-master bus, which for industrial applications, railway applications, stage light control, traffic lights and long distance communication uses a cable with 4 conductors connected as a balanced 4-wire line (X-coupled) to prevent mutual coupling to other cables. The name also refers to the Max-i-mum performance, which by far exceeds comparable fieldbus systems on most fields.
Released specifications can be downloaded from the Technical Description page and used free of charge for all non-commercial use. Commercial use requires membership of Max-i Association.
News
Interface/control module Max-i IF2, overlay module LS1 with 3D printet enclosure for control of two lamps or group of lamps and modem module MD1 have been released.
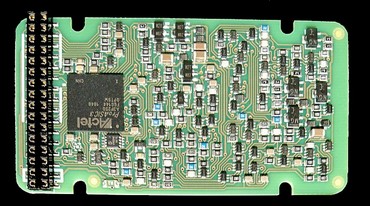
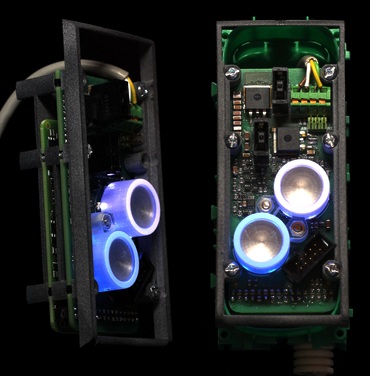
Specification 16.0 has been released.
- Maximum length of attributes changed from 32 to 36 bits and programming optimized according to this.
- Enhanced timeout timer for groups with decisecond resolution.
- Serial number format changed.
- Variable speed added to AD-converter.
- SPI clock changed from fixed frequency to follow the communication speed.
- Automatic saving of hour counter changed to global save command in case of low (battery) voltage.
Max-i Association
C/O Innovatic
Bøgebakken 3, Gjessø
8600 Silkeborg
Denmark
Phone: (+45) 86 84 72 92
E-mail: mail@innovatic.dk
Chairman Carsten Kanstrup
Mobile: (+45) 20 15 51 60
E-mail: ck@innovatic.dk
This page is created with WebSite X5 and updated August 29th 2025