Technical Description
Comparison between CAN and Max-i
Max-i is very similar to CAN, which is probably the only other event driven multi-master bus based on bit-wise bus arbitration except for the old, obsolete STL-Net, but as can be seen from the table below, Max-i is not just much cheaper, but also much more powerful, reliable and safe.
Comparison between CAN and Max-i | CAN | Max-i |
Economy | ||
Possibility for single chip interface | Need CPU and PS | Yes |
Product certification and registration needed | Most protocols | Not necessary |
Use of unshielded, standard installation cables | No | Yes |
Maximum practical power transfer per segment | 384 W at 24 V 1) | ≥1 kW at 20 V 1) |
Maximum practical number of devices per bus | 64-127 | ≈1000 |
Environment | ||
Power saving mode / sleep mode (≤0.5 mA) | Only partial network | Not necessary |
Group control | No | 255 groups |
Data | ||
Multiple master bus with bit wise bus arbitration | Yes | Yes |
Publisher/subscriber model | Partly 2) | Yes |
Identifier length | 11 or 29 bit | 12 or 31 bit |
Multiple use of same identifier | No 3) | Yes 3) |
Number of addressing modes per identifier | 1 | 4 |
Local and global data and global poll of local data | No | Yes |
Possibility for temporary change of values | No | Yes 4) |
Maximum number of bytes | 8 | 1028 or infinite |
Different data to more devices in same telegram | No | Yes 5) |
Specified layers of OSI 7-layer model | 1, 2 | 1, 2, 3, 4, 6, 7 |
Setup attributes per I/O (OSI layer 6) | 0 | 16-1024 |
Reliability | ||
Unshielded cable | No | Yes |
No termination resistors = high failure tolerance | No | Yes 6) |
No bias distortion at capacitive loads | No 7) | Yes 7) |
Ideal triggering level not affected by attenuation | No 8) | Yes 8) |
Line-ringing between devices during arbitration | High, but damped | Low (short pulses) |
Sensitivity to voltage drops in negative supply | High 9) | Low 9) |
Uncritical timing on all bus length and no setup | No | Yes |
Timing not affected by galvanic separation | No | Yes |
Tolerant to contact or conductor failure | No | Up to 2 contacts 10) |
Contact fritting | No 11) | 0.15 - 0.2 µm 11) |
Typical transmitter power / total power loss | 0.2 W / 0.4 W | 3.4 W / 1.3 W 12) |
Receiver hysteresis | 0.1-0.2 V | ±1 V, 3-level |
Sensitivity to vibrations and low temperatures | Crystal oscillator | RC oscillator |
Safety | ||
Error detection | 15-bit BCH 13) | 20-bit CRC |
Protection against masquerading | No | 7-bit Hamming code |
Detection of wrong number of telegrams | No | 7-bit serial number |
Predictable response time | No | Yes, deterministic |
Designed for IEC 61508 SIL 3 | No | Yes |
Speed | ||
4-bit/20-bit polled values/s on 1 km line | 612 / 530 | |
4-bit/20-bit polled values/s on 1.5 km line (1.5 times slower) | 480 / 350 14) | |
4-bit/20-bit event driven values/s on 1 km line | 1136 / 880 15) | |
4-bit/20-bit event driven values/s on 1.5 km line | 480 / 350 14) | |
4-bit/20-bit polled values/s at maximum speed | 9800 / 8472 | 30500 / 17600 14) |
4-bit/20-bit event driven values/s at max. speed | 18176 / 14080 15) | 30500 / 17600 14) |
1) 1500 W requires 5 x 4 mm2 flat cables with power supply from both ends. For the 384 W power level, CAN requires a very expensive thick DeviceNet cable (12.2 mm with 15 AWG / 1.65 mm2 conductors for DC).
2) CAN uses the publisher/subscriber model, but many protocols such as DeviceNet and CANopen need to establish a communication channel between devices before communication can take place and may even divide the network into masters and slaves.
3) Without this feature, it is not possible to make for example multi-way landing switches for LED lighting, and it is not possible to have more control buttons for the same process function or the same function in for example coupled trains, but most (all) CAN protocols such as DeviceNet and CANopen actually has a feature to prevent multiple use of the same identifier!
4) Most process values use 4, 20 or 36 bits, and it is possible to change a value temporary, which can save a lot of time during commissioning for example in case of sensor errors, to try an alarm limit or to simulate the presence of material.
5) Max-i can send individual 8-bit, 16-bit, 24-bit or 32-bit values to more devices in a common telegram with up to 1028 bytes and in this way ensure 100 % data synchronization and a very high efficiency for example for motion control, positioning systems and for stage light where Max-i with advantage can replace DMX512. Standard CAN (not CAN FD) is only able to transmit 8 bytes in each telegram.
6) In Max-i, the traditional termination resistors have been replaced by voltage clamps in each device. This gives a very high failure tolerance as the bus may be cut in any number of parts and each part can still work if it is powered up! This makes it very easy to make an error tolerant loop. The loop just needs to be power supplied from both ends as shown in the page: "Green Smart House Solution" and a error detection unit with two channels must then be connected to the two ends of the communication line. During normal operation, the two channels will receive the same massages and the error detector needs not to do anything, but if a message is only received on one channel, an error should be reported and the message should be repeated on the other channel so that the communication between all devices is preserved. A simple poll for group 255 (all devices) is then enough to find the approximate error location. The voltage clamps also reduce the ringing between devices during bus arbitration, reduce the power loss in the line termination to approximately the half compared to termination resistors and they utilize the reflections to improve the signal waveform and prevent bias-distortion due to noise rectification.
7) Bias distortion occurs in case of capacitive loads or lines if the output impedance of the circuit, which drives the line high, is not the same as the circuit, which drives the line low, as it is the case with CAN, where the line is driven high by a driver with a low impedance, but driven low by two 120 ohm termination resistors in parallel. This may cause a kind of signal rectification where it takes much longer time for a signal to go low than to go high, which destroys the signal integrity and makes it very difficult to chose the right triggering level. In Max-i, the driver is fully symetrical so even very high capacitive loads does not affect the communication.
8) Many fieldbus systems, which use termination resistors including CAN, have the problem that the low level is always 0 V, but the high level depends on the signal level and any attenuation. This makes it even more difficult to select the right triggering level. If the level is chosen too high, a high level may not be recognized in case of attenuation, and if the level is too low, the bus will be very sensitive to noise and it may take too long time for the signal to go low in case of bias distortion. In Max-i, the high signal level is always equal to the low signal level just with opposite sign, so the ideal triggering level is always in the middle no matter how much the signal is attenuated. This makes the signal/noise level even better in practice compared to other fieldbus systems. Below the very critical detection of a recessive CAN bit during bus arbitration is compared to the completely uncritical detection of a Max-i bit:
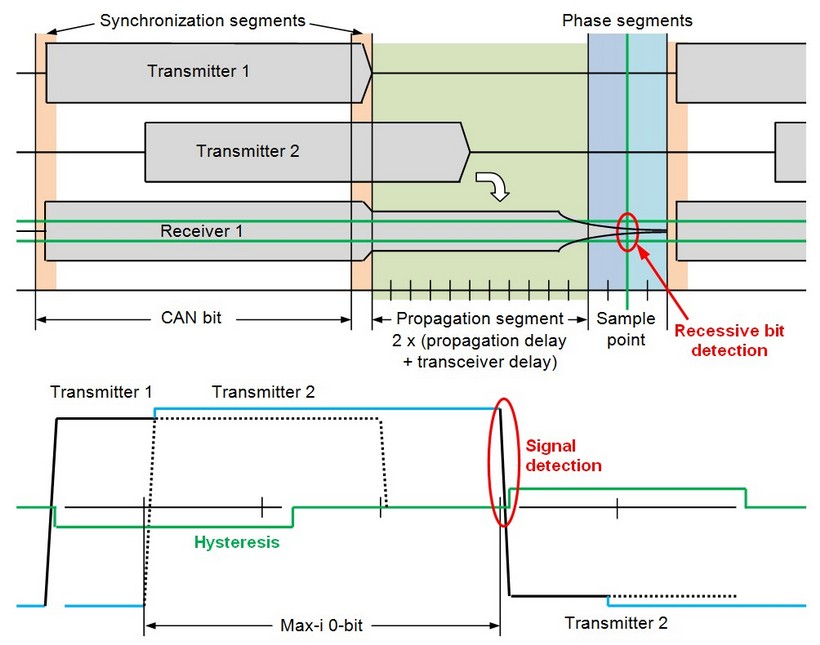
9) The CAN transceiver is usually connected to the negative supply line so even though for example DeviceNet has two power supply lines in the cable for 0 and +24 V, they should not be used for driving heavy loads like actuators and lamps as any voltage drop in the negative supply line will cause bias distortion. Max-i uses the midpoint between the power supply lines as 0-V reference, but must then require that the voltage drop in the two lines are approximately the same, which in practice means that they must have the same cross section.
10) In case of a balanced 4-wire line, where the two communication conductors are connected together in all devices, Max-i will usually survive a failure on one of these conductors or connectors. If more power supplies are used, Max-i may also survive a failure on one of the supply lines so that Max-i is able to survive a failure on two neighbor conductors or connectors.
11) Usually, a fritting voltage of approximately 100 V/µm is required to burn through contact corrosion. Since the supply and communication voltage of Max-i is approximately 20 V, approximately 0.2 µm can be accepted. Below 3-5 V, no fritting can be expected. This makes CAN inexpedient for connections between for example tractors and trailers (trucks) and between train wagons.
12) When a transmitter is activated, two waves are generated with a typical power of 3.4 W in each direction. Because Max-i does not use any termination resistors, the current in each wave falls to zero after the time it takes for the wave to travel to the end of the line and back again to the transmitter. If for example a device is placed in the middle of the line, the two waves will arrive simultaneously, so the power will fall from a total of 6.8 W to zero after a time corresponding to the propagation delay of the line. If the device is placed at the end of the line, one wave arrives immediately, so the power falls from 3.4 W to zero after a time corresponding to two times the propagation delay. No matter where a device is located on the line, the energy (power multiplied by time) is the same, and if the line is shorter than the maximum length, the energy is reduced correspondingly. This reduces the emitted noise and enables battery operation and operation in explosive atmosphere. The power loss in the transmitter and the clamps depend on the supply voltage and the sum is maximum at maximum voltage.
13) In CAN, two bit errors may on rare occasion remain undetected when the first generates a bit stuffing condition and the second then removes a stuff condition (or vice versa), shifting the position of the frame bits between the two bit errors. The shifted area may lead to a burst error that is too long for the CRC mechanism.
14) In Max-i, it does not take longer time to poll a value than to transmit it event driven as the first and last part of the telegram are just transmitted by two or more devices.
15) Because CAN does not have any "babbling idiot" protection, it is not possible to reach this number of telegrams in practice without a completely unpredictable delay of low priority telegrams. Max-i may run even at 100 % and is faster than CAN for safety telegrams where CAN needs an extra layer and it is much faster if the possibility for different data to more devices in the same telegram is utilized as it is the case for stage light and motion control systems.
If you like CAN, you will love Max-i.
Specification
The Max-i specification can be downloaded here: www.max-i.org/specification.pdf
This page is created with WebSite X5 and updated April 24th 2025