Railways and Trucks
Traditional Bus Systems
Many trains like the Danish IC4 and IC2 use the IEC 61375 Wire Train Bus (WTB) as a backbone to connect different vehicles or trainsets and Multifunction Vehicle Bus (MVB) to connects individual nodes within a vehicle or in a closed train set. There are however a lot of problems with this solution compared to Max-i:
- Both WTB and MVB are a master-slave bus systems, which cause a lot of problems:
- Since there can only be one master, it is very difficult to use more control panels and connect debuggers. In case of an error on the active control panel, it may take several seconds to transfer the control to another panel and during that time, the train may be completely out of control at a speed of maybe 200 - 300 km/hour! Max-i is a multiple master bus, so any number of control panels (and debuggers) may be connected, and they will always be fully redundant and may be used to operate the train. The commands are the same no matter from which control panel they are issued and because of the publisher/subscriber model, all nodes and panels will receive the commands and be updated simultaneously within less than a µs.
- WTB needs a very complicated inauguration procedure when trainsets are connected or disconnected or the master fails. The master shall always have the address 01, and devices against the “top” (direction 2) shall be numbered in ascending order and devices against the “bottom” (direction 1) shall be numbered in descending order (Bottom … 61, 62, 63, 01, 02, 03, 04 … Top). If there are more devices in each vehicle or vehicles with no nodes, the applications may even operate with its own different addresses in forward and backwards direction making the system extremely difficult to overlook (bottom and top may not be the same as front and back). This system may work in case of a single locomotive; but it is hopeless in case of connected trainsets. Every time two trainsets need to be connected or disconnected, a very big part of the train needs to be renumbered and a master needs to be removed or created. This has caused so many problems for IC4 and IC2 that even after several years it has not been possible to connect more than 3 trainsets and the expensive platform extensions to 4 trainsets are wasted. With Max-i, it would from the start have been possible to connect any number af trainsets in any order (front against front, front against back and back against back), so there would have been no need for the Multiple-2 and Multiple-3 packages for 2 and 3 trainsets, and there would be no need for renumbering as it uses the trainset numbering directly as shown and described below.
- The efficiency is very low as all sensors needs to be polled all the time. Max-i is basically event driven, but can also be polled.
- WTB can only handle 32 nodes so one or more gateways to MVB are necessary for almost any function (MVB handles the function). Max-i has virtually no such limitations and can replace both WTB and MVB so all vital functions including traction control may be connected directly - not through MVB or a gateway, which highly simplifies the system and debugging and increases the reliability and safety considerably.
- WTB sends individual messages to all train sets, which may even have to be further transfered by MVB. This makes it impossible to control all motors exactly simultaneously, which may create uneven acceleration and be a problem during braking. When the air brakes are activated, the control system should be so fast, that the motors are in idle state before the brake shoes get in contact with the wheels. Besides, it makes it necessary with a fairly long timeout/watchdog time, which increases the distance a train can run without control and therefore reduces the safety. A safety system must always go to a safe state in case of a communication failure. Max-i use the much more efficient publisher/subscriber model where all commands are received exactly simultaneously in all train sets, and it is not necessary with MVB for vital functions. Max-i may even be used for brake-by-wire systems based on electric friction brakes and in this way remove the necessity for air piping and pneumatic components.
- Both WTB and MVB need termination resistors, and in case of WTB, they must be disconnected when trainsets are connected and added when trainsets are disconnected. Max-i uses voltage clamps in all devices instead of termination resistors so there is no terminations to connect or disconnect.
- WTB needs two channels (main and auxiliary), a relay with 4 contacts, 2 termination resistors and a direction switch per bus (A and B) in each node to be able to handle the inauguration procedure and connect the termination resistors. This makes each node very expensive and the signal has to pass many relay contacts, which reduces the reliability. Only one Max-i channel and no contacts are necessary per bus except for the switches (or relays) between trainsets, and when the IC is ready, a Max-i node will only cost a fraction of a WTB or MVB node and be much smaller.
- Both WTB and MVB use RS-485 signal levels with Manchester coding. This reduces the typical drive power to approximately 243 mW (5.4 V differential) on a 120 Ω line, and at the standard speed 1 Mbit/s (2 MBaud), the energy in each pulse Eb is only 120 nJ, which limits the signal/noise ratio. The low voltage makes it necessary with gold plated contacts for a reliable communication since the voltage is too low to cause any contact fritting after the initial fritting/mating, but gold plating will wear off quickly. With the special railway communication based on a precision 24 V power supply in each end of a vagon, the communication voltage is approximately 22 V plus 11 V during reflections, which is 1.7 times higher than the standard communication voltage of 13 V peak-peak. This gives a drive power is 9.7 W on a 50 Ω balanced 4-wire line, which is 40 times more than WTB and MVB, and even without additional fritting it can handle contact corrosion up to approximately 0.3 µm during reflections (fritting voltage 100 V/µm) and may therefore use much more rugged silver contacts. Since Max-i does not use any termination resistors, the transmitter only draws current until the reflections arrive, so the average power loss is only a fraction of the 9.7 W depending on the line length. Probably no other fast fieldbus offer a better efficiency and signal/noise ratio than Max-i!
- WTB only has a 16-bit CRC check, which is hardly enough for safety applications, and MVB, which handles most functionality, has only 8 check bits, which is not enough for safety critical applications without additional layers! Max-i uses 20 CRC bits plus a 7-bit Hamming code on the identifier to protect against masquerading and may even use a 7-bit telegram serial number to be able to detect lost and inserted telegrams.
- WTB and MVB need software assistance, which reduces the reliability considerably and makes the system much less predictable. As a consequence, the requirements in the IEC 61508 safety standard, which is the mother standard for the railway standard IEC 62279, is 10 times higher for a software solution for a given SIL level than for a hardware solution. In Max-i, most basic functions including transfer of Boolean 4-bit safety values are handled entirely in hardware, which cannot go down like a program, and it uses a rugged RC-oscillator (not a crystal) and a unique dual phase clocking scheme for absolute maximum reliability and tolerance to single event upsets (SEU) and changes in transistor data over time and temperature. This also makes Max-i suitable for even the most demanding space applications!
Max-i Alternative
Below is a drawing of how a Max-i solution for trainset connections may be implemented with two redundant bus systems (A and B), which are also used to define what is right and left in the train and with that the direction of movement:
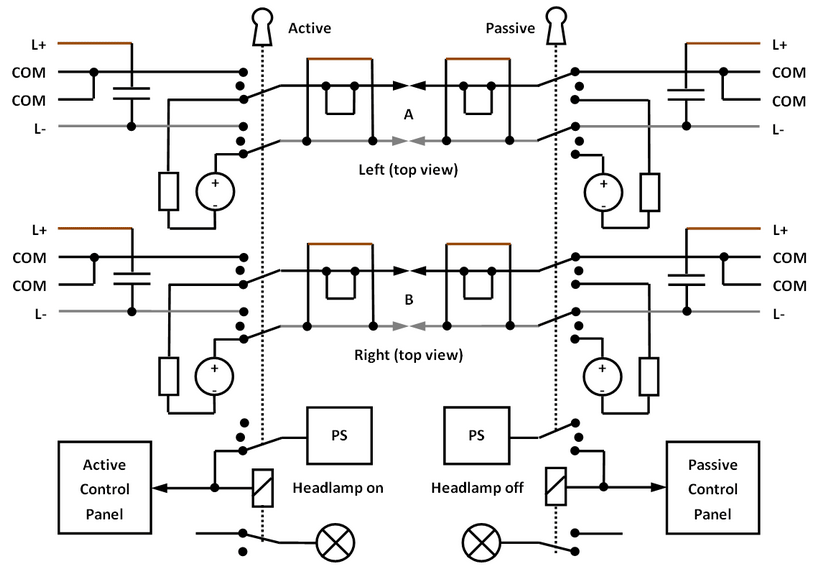
A key switch in each control cabin/panel is used to control the circuit, but many other solutions with relays etc. are possible. To maintain the line balance and line impedance, the connection from the switch to the train coupling shall also be a balanced 4-wire line where conductor 1 and 3 are connected directly together in the same way as conductor 2 and 4 (COM), and to ensure a reasonable symmetrical line clamping, all power supplies shall be placed close to the connection point and have high accuracy as specified in the Max-i specification.
The key switch must be activated in the control panel in the front of the train, that is, in the direction of movement. This:
- Defines what is right and left in the train by transmitting “Right” commands on the B bus and “Left” commands on the A bus.
- Activates the control panel.
- Enables the headlamps.
- Disconnects the bus from the front coupling so that a following coupling process does not disturb the communication in the trainset, which moves.
- May connects the electrical connections in the front coupling to a fritting voltage in the order of 50 V in series with a resistor, which shall limit the current to less than 50 mA and ensure at least 1 kΩ impedance to the COM conductors (no capacitive load). Note that depending on the contact material this may not be necessary if the special railway mode is used as the signal itself generates a fritting voltage of 33 V, which is even present all the time and not just during train connection! This further simplifies the system compared to WTB where a fritting generator is absolutely necessary for a reliable communication.
To connect two trainsets as shown on the drawing, a moving trainset is connected to the back of a trainset, which does not move and therefore has no (vital) communication on the line. In the back end, the switch is in passive state and L+ and COM are therefore connected to the electrical connections in the train coupling. When the electrical connections between the two trainsets are made, the COM voltage is pulled low by the fritting circuit and clamped to the negative clamp voltage, but because the idle line state is low, the line state does not change. The engineer then switches the control panel in the middle (previously front) off and the two busses get connected so that both trainsets can be controlled from the control panel in the front when it is activated (may be that already). Note that the fritting generator only needs to be active in the active/moving part, which makes it possible for the passive part to be powered down, but in that case, it may be necessary to add an additionally negative clamp circuit as the internal clamp circuits in the devices may be in high impedance state.
In case of dead wagons, that is, wagons, which are not powered up and therefore do not have working terminations, the switch in the front shall be in the middle position if the wagon is the last one in the train. In this way, a long unterminated cable-end is avoided. If the dead wagon is not the last one in the train, the switch shall be in the passive position to pass the communication through.
To be able to address the various signals, Max-i uses its identifier in the following way:
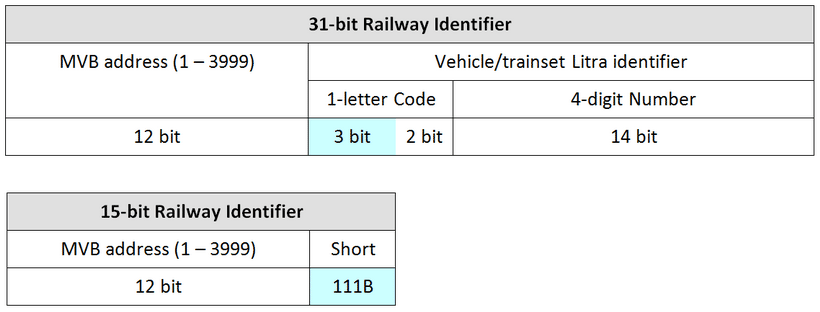
The identifier is a combination between the Litra codes where only the first Litra letter, which defines the main group, is used, and the 12-bit MVB address so that each signal in connected trainsets can be uniquely identified. For maximum efficiency, the short identifier may be used internal in a trainset and gateways to the two backbone busses A and B may then insert or remove the shortened Litra number. In this way, Max-i can replace MVB without the need to renumber the signals.
Trucks and Trailers
A similar implementation may be used for trucks and trailers; but there is no need for a switch in the trailer as there is no driver’s cab so it can always be passive. The switch in the truck is put in the active position when the truck is backed towards the trailer (driver’s cab may be regarded as in the back of the truck) and set in the passive position when the two parts are connected (driver’s cab in the front of the truck).
This page is created with WebSite X5 and updated April 25th 2025.